What is Porosity in Welding: Secret Aspects and Their Influence On Weld High Quality
Comprehending Porosity in Welding: Checking Out Causes, Impacts, and Avoidance Methods
As experts in the welding sector are well conscious, recognizing the causes, effects, and prevention strategies connected to porosity is essential for achieving robust and dependable welds. By delving into the root creates of porosity, examining its harmful results on weld high quality, and exploring effective prevention techniques, welders can boost their knowledge and skills to create high-quality welds continually.
Common Reasons For Porosity
Contamination, in the type of dirt, oil, or rust on the welding surface, creates gas pockets when warmed, leading to porosity in the weld. Inappropriate protecting takes place when the protecting gas, generally utilized in processes like MIG and TIG welding, is incapable to completely safeguard the molten weld pool from reacting with the bordering air, resulting in gas entrapment and subsequent porosity. In addition, insufficient gas insurance coverage, usually due to wrong circulation rates or nozzle positioning, can leave parts of the weld unprotected, permitting porosity to develop.
Results on Weld Top Quality
The existence of porosity in a weld can substantially jeopardize the general high quality and honesty of the bonded joint. Porosity within a weld develops gaps or tooth cavities that weaken the framework, making it a lot more susceptible to fracturing, corrosion, and mechanical failing.
Furthermore, porosity can prevent the efficiency of non-destructive screening (NDT) techniques, making it challenging to identify various other issues or suspensions within the weld. This can lead to substantial security issues, especially in crucial applications where the architectural integrity of the bonded parts is critical.

Prevention Techniques Summary
Given the detrimental influence of porosity on weld quality, effective avoidance strategies are crucial to keeping the architectural stability of bonded joints. Furthermore, picking the appropriate welding parameters, such as voltage, present, and take a trip speed, can aid lessen the danger of porosity formation. By incorporating these avoidance methods right into welding methods, the event of porosity can be significantly reduced, leading to stronger and much more dependable welded joints.
Significance of Proper Protecting
Correct protecting in welding plays an important function in avoiding atmospheric contamination and making certain the integrity of welded joints. Protecting gases, such as argon, helium, or a mix of both, are commonly used to safeguard the weld pool from reacting with components airborne like oxygen and nitrogen. When these responsive elements enter call with the warm weld pool, they can create porosity, bring about weak welds with lowered mechanical residential properties.

Inadequate protecting can lead to different problems like porosity, spatter, and oxidation, jeopardizing the architectural stability of the welded joint. For that reason, adhering to appropriate securing techniques is vital to create high-grade welds with marginal issues and ensure the longevity and integrity of the welded elements (What is Porosity).
Monitoring and Control Techniques
How can welders properly keep an eye on and control the welding procedure to guarantee optimal outcomes and prevent issues like porosity? By continuously monitoring these variables, welders can determine deviations from the perfect problems and make prompt adjustments to avoid porosity formation.

In addition, implementing appropriate training programs for welders is necessary for monitoring and controlling the welding process efficiently. What is Porosity. Enlightening welders on the relevance of maintaining consistent specifications, such as proper gas shielding and take a trip rate, can assist stop porosity problems. Regular assessments read the article and qualifications can additionally guarantee that welders are efficient in tracking and managing welding processes
In addition, making use of automated welding systems can improve tracking and control abilities. These systems can exactly control welding specifications, lowering the likelihood of human error and ensuring regular weld quality. By incorporating innovative tracking technologies, training programs, and automated systems, welders can properly keep track of and control the try these out welding process to minimize porosity issues and accomplish top quality welds.
Conclusion
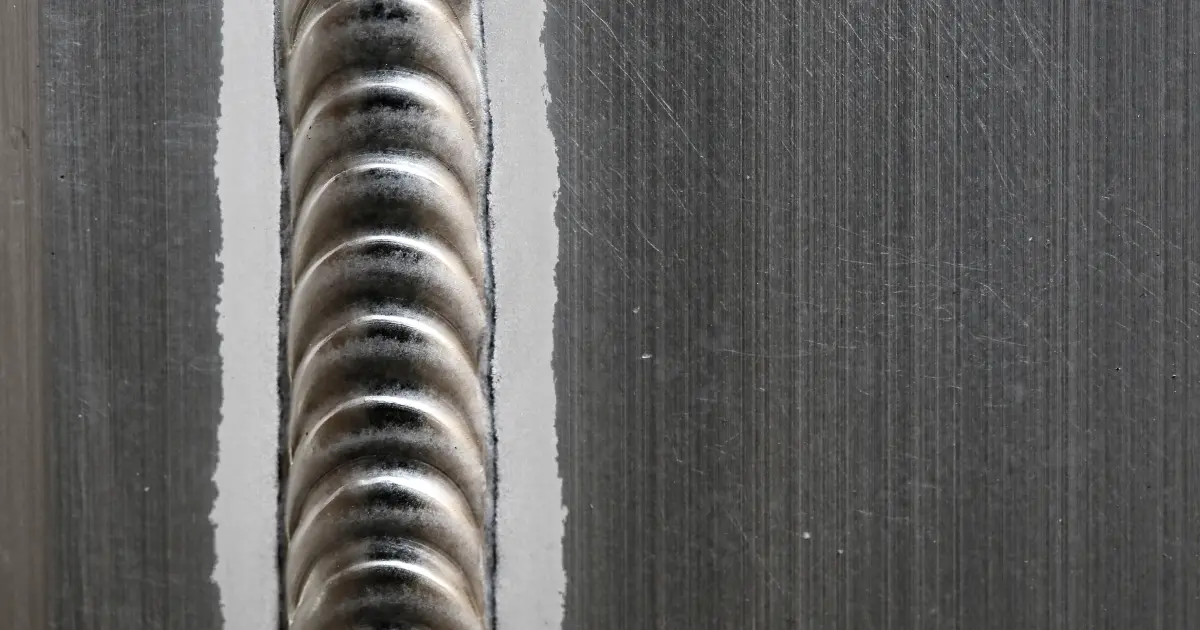